SMT has revolutionized the electronics manufacturing industry by enabling the efficient placement of components onto printed circuit boards (PCBs). Central to this process is SMT placement equipment, which plays a crucial role in automating and optimizing the assembly of electronic devices.
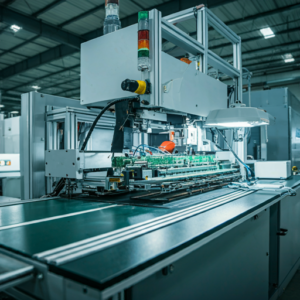
What is SMT Placement Equipment?
SMT placement equipment refers to machinery designed to precisely place surface-mount components onto PCBs. These machines operate with high accuracy, ensuring that the components are positioned correctly according to the design specifications. The speed and precision of SMT placement equipment have made it indispensable in producing modern electronic devices such as smartphones, computers, and various industrial electronics.How Does SMT Placement Equipment Work?
The operation of SMT placement equipment is typically automated. The process starts with a PCB being fed into the machine, followed by component identification and placement. The equipment uses advanced vision systems to detect component orientation and positioning, ensuring the components are accurately placed onto the solder paste-applied areas of the PCB. Once positioned, the PCB moves on to the soldering process, where the components are permanently fixed.Benefits of Modern SMT Placement Equipment
The latest advancements in SMT placement equipment have brought several key benefits to the manufacturing industry:- Higher Precision: Advanced vision systems and robotic arms allow for extremely accurate component placement, reducing errors and rework.
- Increased Speed: Modern equipment can place thousands of components per hour, drastically improving production throughput.
- Flexibility: These machines are highly versatile and capable of placing a wide range of component sizes and types, making them suitable for various manufacturing requirements.
- Reduced Labor Costs: The automation provided by modern SMT placement equipment minimizes the need for manual labor in the assembly process. This not only lowers labor costs but also reduces human error, resulting in higher consistency and product quality.
- Scalability: As demand increases, manufacturers can scale their operations more easily with SMT placement equipment. The machines can be adjusted to handle larger production volumes without compromising on speed or precision.
- Enhanced Reliability: These machines are designed for continuous operation with minimal downtime. Their reliability ensures smooth production runs, helping manufacturers meet deadlines and maintain consistent output.
- Improved Component Handling: The latest SMT placement equipment can handle delicate and fragile components with care, reducing the risk of damage during assembly. This is particularly important for high-tech industries such as aerospace, medical devices, and telecommunications.
- Real-Time Monitoring and Data Analysis: Many modern machines are equipped with real-time monitoring systems that provide detailed data on the production process. Manufacturers can track key metrics like placement accuracy and machine performance, allowing for quick adjustments and optimization of the production line.
Trends in SMT Placement Equipment
The development of SMT placement equipment continues to evolve, with a few notable trends emerging:- Automation and AI Integration: Incorporating AI algorithms into the equipment allows for smarter decision-making during the placement process. Automated diagnostics can detect potential issues before they affect the product quality.
- Miniaturization: As electronic devices become smaller, SMT placement equipment is evolving to handle miniature components more efficiently, without compromising on speed or accuracy.
- Sustainability: There is a growing focus on energy-efficient SMT placement equipment that reduces power consumption and minimizes waste during the production process.