Welding defects are a frequent challenge in the sheet metal welding process and can significantly impact the quality and functionality of final products. Addressing these issues requires understanding their root causes and employing effective solutions to mitigate them.
One of the most common defects in the sheet metal welding process is porosity, which results from trapped gas bubbles within the weld. Porosity can weaken the weld and reduce its durability. To avoid this issue, proper cleaning of the metal surface is essential to remove contaminants such as oil, dirt, and moisture. Additionally, optimizing shielding gas usage during the welding process minimizes gas intrusion.
Cracks are another prevalent defect observed in the sheet metal welding process. These can occur due to excessive stress or improper cooling. Controlling heat input and cooling rates is crucial to preventing cracks. Pre-heating the sheet metal and using suitable filler materials also reduces stress concentrations and enhances weld integrity.
Undercutting, where grooves are formed along the edges of the weld, is another defect that can weaken the joint. In the sheet metal welding process, maintaining correct welding speed and electrode angles helps minimize undercutting. Adequate skill training for welders ensures better control and precision during operation.
Incomplete fusion, where the weld metal fails to fully penetrate the base metal, can compromise strength. To address this issue in the sheet metal welding process, it’s important to adjust welding parameters such as voltage and current. Proper joint preparation and positioning are equally critical for achieving complete fusion.
Lastly, distortion is a common concern in the sheet metal welding process, especially with thin materials. Techniques like staggered welding, clamping, and heat management are effective in minimizing distortions and ensuring product accuracy.
In summary, tackling welding defects in the sheet metal welding process involves cleaning surfaces, optimizing welding parameters, and applying preventive techniques. By focusing on these aspects, manufacturers can achieve stronger and more reliable welds.0
One of the most common defects in the sheet metal welding process is porosity, which results from trapped gas bubbles within the weld. Porosity can weaken the weld and reduce its durability. To avoid this issue, proper cleaning of the metal surface is essential to remove contaminants such as oil, dirt, and moisture. Additionally, optimizing shielding gas usage during the welding process minimizes gas intrusion.
Cracks are another prevalent defect observed in the sheet metal welding process. These can occur due to excessive stress or improper cooling. Controlling heat input and cooling rates is crucial to preventing cracks. Pre-heating the sheet metal and using suitable filler materials also reduces stress concentrations and enhances weld integrity.
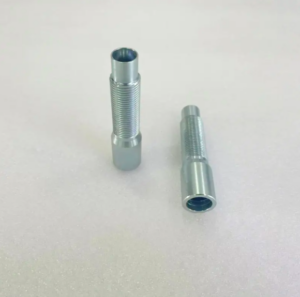
Undercutting, where grooves are formed along the edges of the weld, is another defect that can weaken the joint. In the sheet metal welding process, maintaining correct welding speed and electrode angles helps minimize undercutting. Adequate skill training for welders ensures better control and precision during operation.
Incomplete fusion, where the weld metal fails to fully penetrate the base metal, can compromise strength. To address this issue in the sheet metal welding process, it’s important to adjust welding parameters such as voltage and current. Proper joint preparation and positioning are equally critical for achieving complete fusion.
Lastly, distortion is a common concern in the sheet metal welding process, especially with thin materials. Techniques like staggered welding, clamping, and heat management are effective in minimizing distortions and ensuring product accuracy.
In summary, tackling welding defects in the sheet metal welding process involves cleaning surfaces, optimizing welding parameters, and applying preventive techniques. By focusing on these aspects, manufacturers can achieve stronger and more reliable welds.0