In CNC machining, surface finishing isn’t just about aesthetics—it directly impacts a part’s performance, durability, and cost. Ambiguous or undefined surface requirements often lead to functional failures, rework costs, and delays. For instance, a poorly specified roughness tolerance might result in parts that underperform or wear prematurely. This blog explores the importance of surface finishing, focusing on roughness as a critical metric, and provides actionable insights for optimizing metal surface finishes.
Common Metal Surface Finishing Techniques in CNC Machining
1. Standard Surface Finishing
- Process: Basic cleaning and deburring, achieving a maximum roughness of Ra 125 micro inches (3.2μm).
- Applications: Cost-effective for non-critical parts like brackets or structural components.
2. Anodizing
- Process: Electrochemical oxidation to create a protective oxide layer on aluminum.
- Benefits: Enhances corrosion resistance, allows dyeing for aesthetics, and improves hardness.
- Types: Transparent Anodizing: Preserves metal’s natural look while boosting durability.
- Hardcoat Anodizing (Type III): Produces thicker, wear-resistant coatings for aerospace and automotive parts.
3. Polishing
- Hand Polishing: Ideal for complex geometries but labor-intensive.
- Machine Polishing: Efficient for high-volume production, achieving mirror-like finishes (Ra ≤ 4 μm).
4. Chemical Treatments
- Passivation: Removes free iron from stainless steel using nitric or citric acid, preventing corrosion.
- Black Oxidation: Forms a magnetite layer on steel for anti-reflective surfaces in tools and firearms.
5. Coatings
- Electroplating: Deposits metals like chrome or nickel for enhanced conductivity and corrosion resistance.
- Powder Coating: Eco-friendly, thick polymer layers for outdoor equipment and consumer goods.
6. Blasting & Texturing
- Sandblasting: Creates uniform matte textures (Ra 1.6–2 μm) for improved paint adhesion.
- Laser Texturing: Precision patterns for functional or decorative purposes.
- Surface Roughness: A Critical Functional Metric
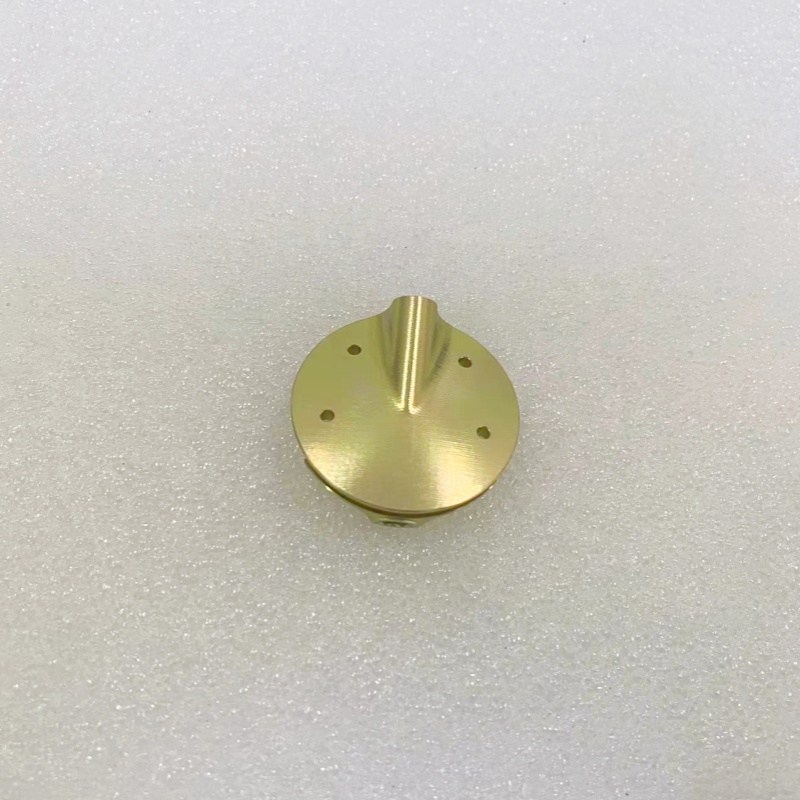
Surface roughness measures microscopic peaks and valleys on a machined surface
quantified using parameters like:- Ra (Average Roughness): Most common for overall quality control (e.g., Ra 0.4 μm for medical implants).
- Ry (Maximum Height): Detects deep scratches or outliers.
- Rz (Mean Roughness Depth): Combines Ra and Ry for comprehensive analysis.
Why Roughness Matters
- Wear Resistance: Smoother surfaces (Ra < 0.8 μm) reduce friction and prolong component life.
- Corrosion Protection: Rough surfaces trap moisture, accelerating oxidation; polished or coated finishes mitigate this.
- Sealing Performance: Hydraulic/pneumatic seals require Ra ≤ 4 μm to prevent leaks.
- Aesthetics: Mirror finishes (Ra ≤ 1 μm) are critical for luxury goods and visible components.
Measuring Surface Roughness in CNC Machining
- Contact Methods: Stylus profilometers (e.g., Mitutoyo Surftest) trace surfaces to calculate Ra/Rz.
- Non-contact Methods: Laser scanners or 3D optical profilers for delicate or complex parts.
- Microscopy: SEM or metallurgical microscopes analyze texture and defects.
Best Practices:
Optimize cutting parameters (speed, feed rate) to minimize tool marks. Use sharp, coated tools (e.g., diamond-coated end mills) for finer finishes. Implement real-time monitoring systems to detect roughness deviations.Case Studies: Surface Finishing in Action
- Aerospace Component: An aluminum turbine blade anodized to Ra 0.2 μm achieved 50% longer service life by resisting saltwater corrosion.
- Medical Implant: Electropolishing stainless steel reduced bacterial adhesion by 70% (Ra 0.4 μm vs. Ra 1.6 μm).
- Automotive Gear: Shot peening followed by black oxidation improved fatigue strength by 30%.
Choosing a Surface Finishing Partner
- Analyze Functional Needs: Match roughness tolerances to the application (e.g., Ra 0.8 μm for engine parts vs. Ra 0.4 μm for seals).
- Optimize Cost-Efficiency: Combine processes like machining + anodizing to reduce steps.
- Ensure Compliance: Adhere to standards like MIL-A-8625 for anodizing or ASTM B117 for salt spray testing.